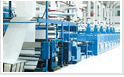
1. The introduction
Hot air tension setting machine is widely used in finishing process of various textiles such as woven fabric, knitted fabric, etc. The equipment has a wide range of functions, strong stability and reproducibility, easy operation, easy maintenance, energy saving, high degree of automation. The production system is a continuous production process, drawing molding machine production process to go through the production process are: first (cloth bucket J cloth, cloth sizing, shaping, baking heating, cloth spray cooling, finally roll molding. In this process, it is necessary to complete the synchronous control of pulling cloth, pulling cloth, constant temperature control in oven, tension control of rewinding and pressure control of the surface of rewinding.
2. Operating principle of tension setting machine system
The process flow chart of drawing and setting machine is shown in Figure 1
Process flow chart of drawing and setting machine
2.1 Cloth the pulp cloth
The cloth starts from the cloth bucket and is pulled by the traction bar, which is driven by a 3.7kW motor driven by a WinMO inverter VFT-0037T4. A VFT0015T4 frequency converter is used to drive the grouting machine for cloth sizing.
2.2 Cloth shaping
According to the width and length of the cloth, the servo machine automatically moves the pins on the left and right cloth feeding wheels to locate the cloth, drives the motor through a brush frequency conversion VFT0007T4 and a cloth frequency conversion VFT0022T4, and sends it to the baking box to bake and set for molding.
2.3 Temperature control
The heating system in the baking box is heated by hot kerosene, and L 0 VFP0150 frequency converter and 2O 7.5KW fan are used for hot air circulation to make the baking box temperature uniform. The temperature of the oven is controlled by adjusting the opening degree of the oil valve of the hot kerosene. The temperature of the oven is detected by 12 sets of temperature sensors. The temperature signal measured is controlled by adjusting the opening degree of the oil valve through PID to realize the constant temperature control of the oven.
2.4 Synchronous traction control
The speed of the cloth in the baking passage is basically constant, and there may be a small range of up and down movement. In this way, a pressure roller must be arranged on the traction rollers at both ends of the baking box (that is, the main traction and the auxiliary traction), so that the tension of the baking box is separated from the tension of the cloth and the winding. The linear speed of the traction chain at both ends of the baking box has a strict proportional relationship to meet the linear speed synchronization. In order to meet the cloth in the baking box tension constant, to prevent cloth in the production of wire drawing, pull off the needle phenomenon. Two VFT0185T4 frequency converters and synchronous card are used to realize synchronous control and meet the technological requirements.
2.5 Spray cooling of cloth
The cloth after the baking box is pressed by the press roller, and the cloth is cooled by the spray faucet to ensure that the cloth has a certain toughness, to prevent discoloration and brittleness to ensure the quality of the product.
2.6 Winding control
The winding part has two kinds of situations: one is to push, is not high requirements for general cloth, direct use of the push frame to roll the cloth into the cloth car, push with a VFT0015T4 frequency converter control to achieve the push function; In the other case, the cloth requirements are high and can not be wrinkled (for high quality export cloth). This paper mainly discusses the central winding, and requires the realization of speed control ratio. After the cloth comes out of the main traction roll, the driving roll, flattening roll, guide roll and contact roll are wound on the central winding roll to complete the forming process of the cloth. The roll core (also known as the mother roll) is generally used only to produce semi-finished products, but also to cut and rewind, and finally rolled into the required small roll finished products. Therefore, its performance and quality directly affect the quality of finished cloth and yield.
2.6.1 Composition of Unwinding Parts
The composition of the reel part is shown in Figure 2.
(1) the flattening roller
The roller into a cylindrical slightly curved shape, according to the winding situation of the flattening roll to adjust the bending degree of the flattening roll to make the cloth flat, eliminate the longitudinal wrinkles of the cloth under the action of tensile stress to make the cloth flat and not deformation.
(2) the contact roller
Above the centre of the winding roll core is equipped with a roll can meet in a wide range of activities, contact roller drive is to use a pneumatic proportional valve to control, its main function is to press the cloth horse depends on center winding roll core, realize contact winding, winding or small clearance to flat piece goods quickly turned into the core winding, the winding formation. The contact roller always depends on the surface of the coiling core cloth with a certain pressure, so as to timely eliminate the air between the layers of the cloth when rewinding, so that the cloth roll does not loose. After using the contact roller, the air content in the cloth roll can be reduced to about 12 ~ 16 %.
(3) the take-up roll
The coiling speed is controlled by A C E 09A controller and 8707 process card. The automatic control of constant tension is realized by A C E E 09A controller.
2.6.2 Influence of tension and pressure on the quality of coils
The size of coiling tension directly affects the quality of products. The tension is too large, the winding is too tight, the cloth is easy to produce wrinkles, and even the phenomenon of wire drawing or pulling off the needle; If the tension is too small, the cloth is easy to slide axially on the central roll core, which is seriously misplaced and untidy. In order to meet the requirements of production process, Danfoss FC300 frequency converter +MC0305 synchronous card is used for constant tension control.
3. The conclusion
The system has been put into operation in June 2012, and the system is in good running condition at present. The system performance is stable, easy to operate, easy to maintain, the system speed, tension, pressure and precision and dynamic response can reach the design requirements. Achieve the industry's consistent high praise.